锂电池电解液是电池性能的核心材料,其合成过程需在高压(通常5~15MPa)、高温(80~150℃)条件下完成,对反应设备的安全性与效率提出了双重挑战。微型高压反应釜凭借体积小、传质效率高、控温精准等优势,成为电解液合成的理想选择,但其安全性与效率的平衡仍是技术优化的关键。
一、安全性:高压环境下的风险防控
微型高压反应釜在电解液合成中需应对高压气体(如CO₂、EC溶剂蒸汽)与高活性锂盐(如六氟磷酸锂)的双重风险。
1.耐压结构设计:采用316L不锈钢或钛合金壳体,通过有限元分析优化壁厚与法兰连接结构,确保承压能力达20MPa以上(远高于常规工作压力),避免超压破裂风险;
2.密封技术升级:金属复合密封圈(如不锈钢+石墨层)与法兰面镜面抛光(Ra≤0.8μm)结合,可承受高压循环(≥1000次)而不泄漏,防止电解液挥发或氢氟酸(HF)腐蚀;
3.智能泄压系统:集成爆破片(阈值设定±0.5MPa误差)与电磁泄压阀,当压力传感器检测到异常升高时,0.1秒内启动泄压,避免超压爆炸。
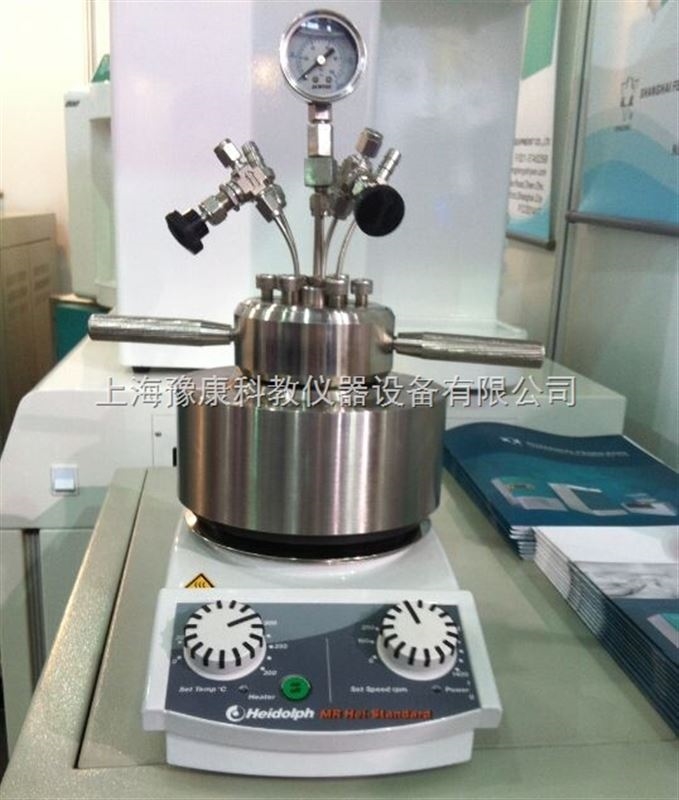
二、效率:高压-高温协同下的反应优化
电解液合成效率取决于传质速率与反应均匀性,微型高压反应釜通过以下设计实现突破:
1.微通道搅拌桨:采用涡轮式+锚式复合搅拌结构,桨叶表面激光雕刻微米级沟槽,可提升局部湍流强度30%以上,使锂盐与溶剂的混合时间从传统反应釜的30分钟缩短至15分钟;
2.高精度温控系统:内置PT100温度传感器与PID控制器,控温精度达±0.5℃,避免局部过热导致电解液分解(如EC脱水生成乙烯碳酸酯副产物);
3.压力-温度耦合控制:通过PLC实时调节加热功率与泄压阀开度,在保证安全的前提下维持最佳反应条件(如10MPa/120℃),使电解液关键指标(离子电导率、水分含量)达标时间缩短20%。
三、未来方向:智能化与标准化
未来微型高压反应釜将向智能化监测与工艺标准化发展:
1.集成在线拉曼光谱或电化学阻抗传感器,实时监测电解液合成中的副产物生成与反应终点;
2.制定高压反应釜安全操作规范(如压力波动预警阈值、密封件更换周期),推动行业安全水平提升。
微型高压反应釜通过结构创新与智能控制,在锂电池电解液合成中实现了安全性与效率的动态平衡,为高能量密度电池的研发提供了可靠保障。随着材料科学与自动化技术的进步,其应用潜力将进一步释放。